Concrete is the most widely used construction material in the world due to its durability and strength. The ease with which it can be molded to form any shape makes it incredibly versatile. However, the success of a construction project depends on more than just its strength – the workability of the concrete mix is equally critical. Workability is the measure of the blend’s ability to be easily placed, compacted, and finished without any segregation. Numerous factors affect the workability of concrete. In this section, we will look at the ten most important factors that influence the workability of concrete.
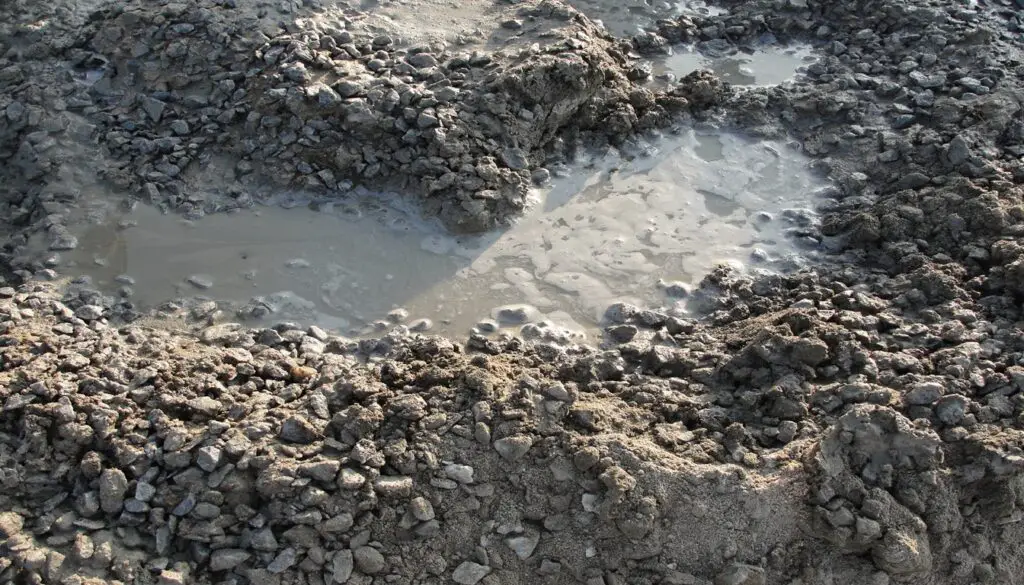
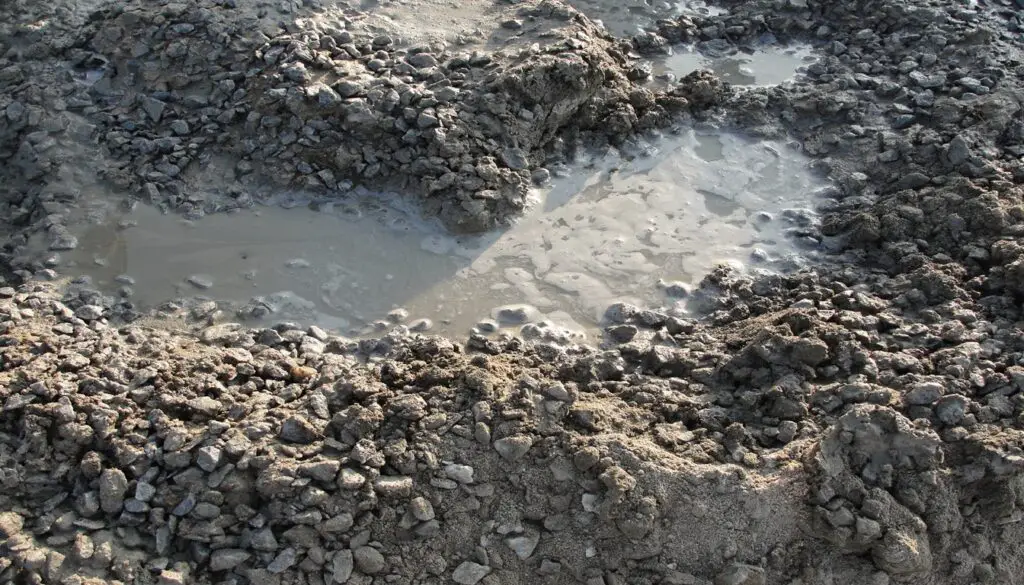
Key Takeaways:
- Workability measures a concrete mix’s ease of placement, compaction, and finishing without any segregation.
- Optimizing concrete workability is critical for the success of construction projects.
- Several factors influence the workability of concrete, including water content, mix proportions, aggregates’ size, shape, grading, surface texture, use of admixtures, use of supplementary cementitious materials, time, and temperature.
- Understanding and controlling these factors are crucial for achieving the desired workability in concrete mixes.
- Construction professionals must choose the appropriate mix proportions, aggregates, and chemical additives to optimize concrete workability.
Water Content
The workability of concrete is heavily reliant on the water content of the mix. The amount of water used can significantly affect the concrete’s consistency and ease of placement. It is crucial to find the right balance in water content to achieve the desired level of workability.
Using too little water can make the mix dry and stiff, which can lead to challenges in placement. On the other hand, using excess water can make the mix too wet, resulting in a decrease in strength and a slump, which can make it difficult to maintain the desired position of the concrete.
To find the right water content for a specific application, a concrete producer should consider factors such as the size and shape of aggregates, the mix design, and the use of admixtures. These factors can all impact the optimal water content to achieve a mix with the desired level of workability and strength.
It is vital to calculate the required water content precisely for each concrete mix to avoid compromising its workability and strength. A skilled professional can determine the amount of water needed to produce the appropriate workability and ensure quality concrete placement.
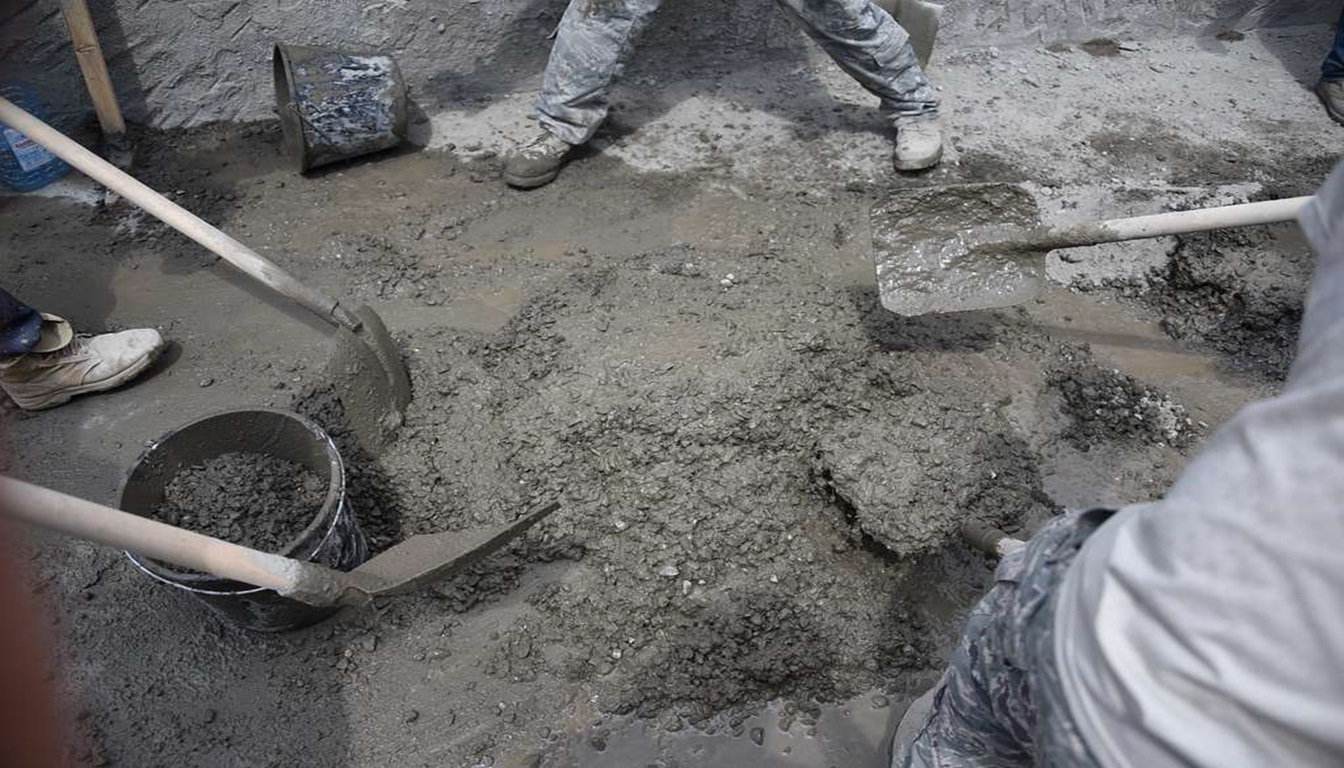
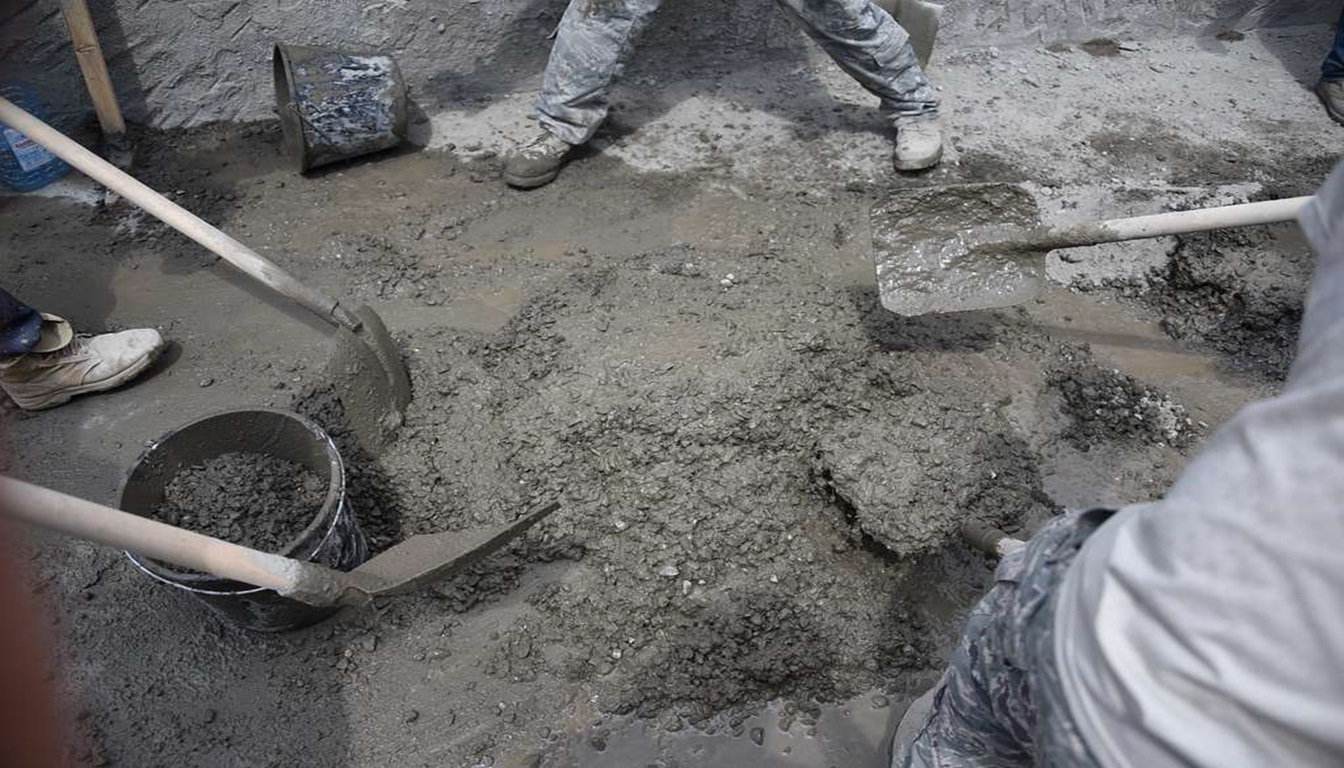
Impact of Water Content on Concrete Workability
Water Content | Concrete Workability Impact |
---|---|
Too little water | Dry and stiff mix, difficult to place, low workability |
Optimal water content | Easy placement, good flow, optimal workability |
Excessive water | Slump, reduced strength, potential cracking, higher risk of segregation |
Table: The impact of water content on concrete workability
Mix Proportions
The workability of concrete is significantly influenced by the proportions of cement, aggregates, and water in a mix. Adjusting the ratios of these components can help achieve the desired flow and ease of placement, which is a key factor in optimizing workability.
Concrete mix design involves determining the appropriate proportions of cement, fine aggregates, coarse aggregates, and water to achieve the desired properties of the mix. The mix proportions are defined based on factors such as compressive strength, durability, workability, and cost. Achieving the desired workability requires careful attention to the selection of appropriate mix proportions.
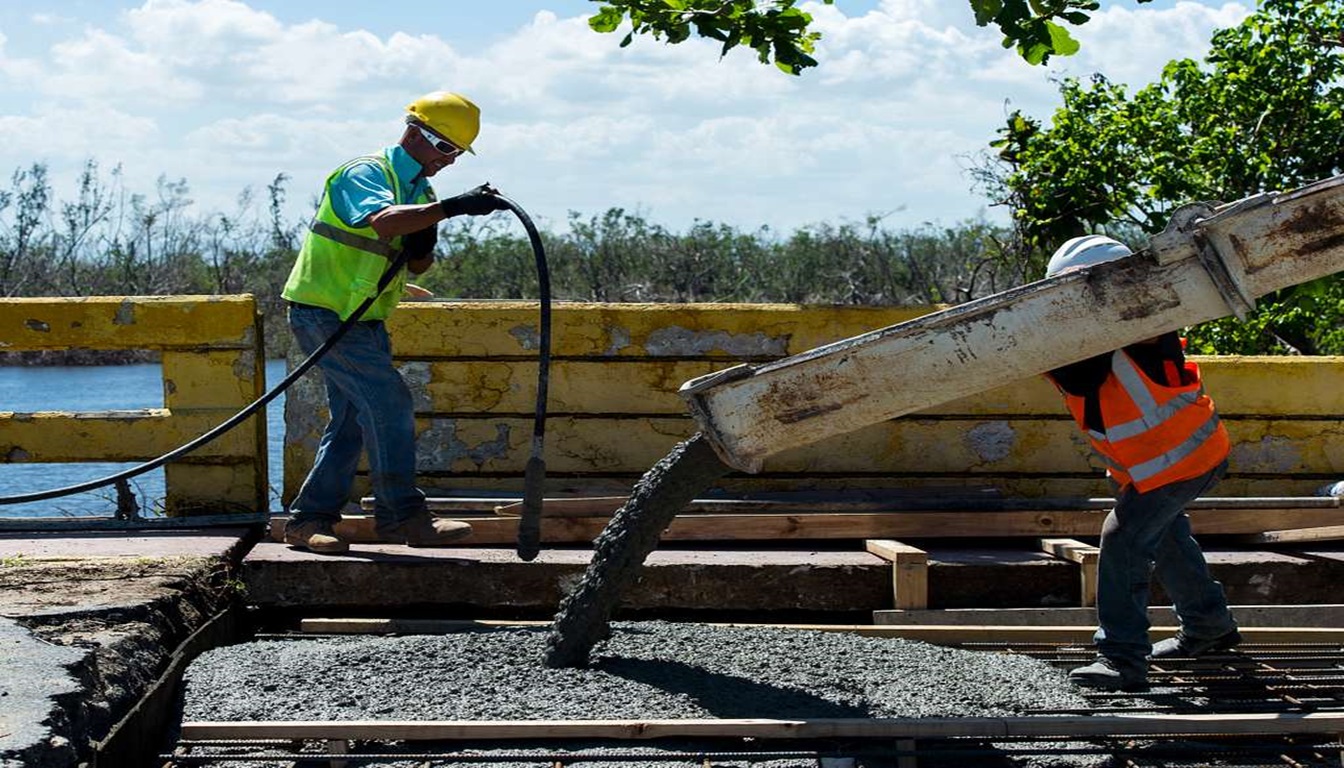
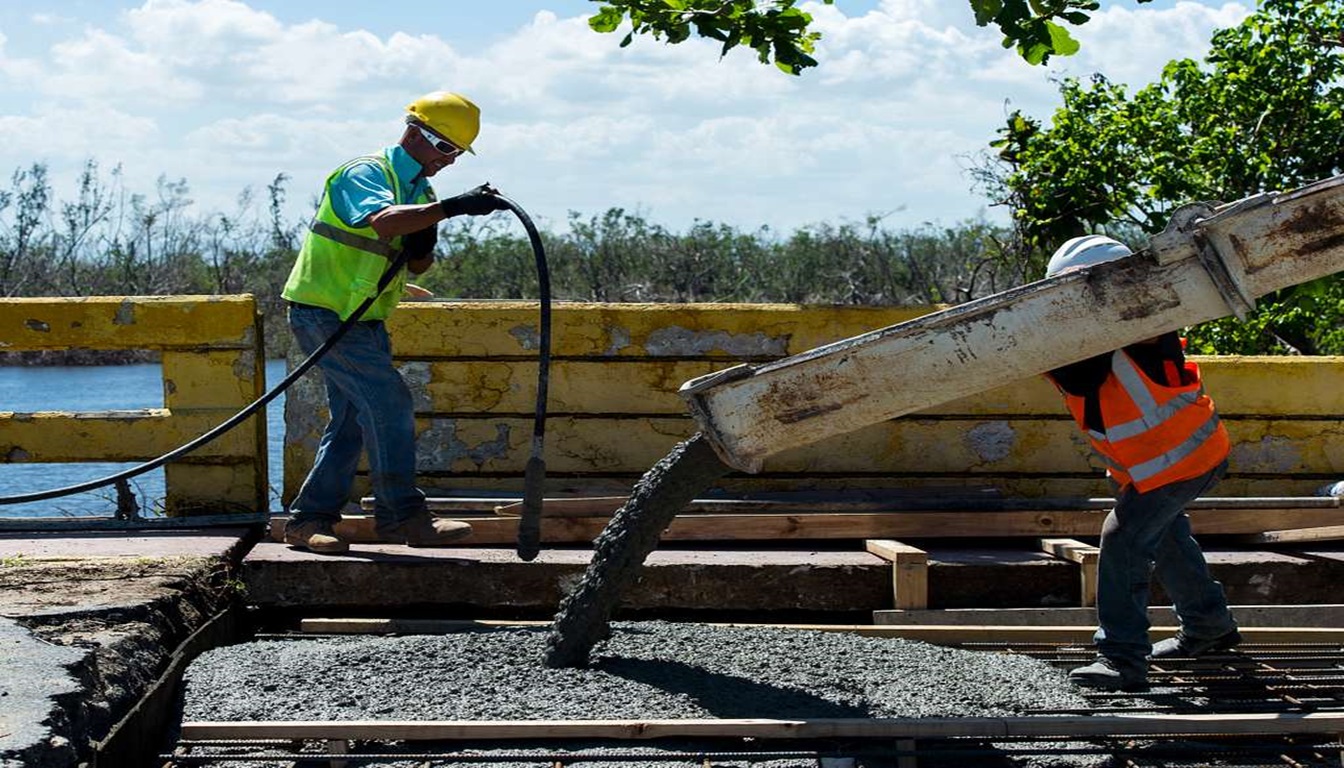
There are various methods for determining concrete mix proportions, including the use of empirical formulas, trial mixes, and computer-aided design. The selection of the appropriate method depends on factors such as the project requirements, materials availability, and the level of sophistication required.
Table 1 illustrates the recommended mix proportions for different grades of concrete as per Indian Standards. These proportions are based on the compressive strength required for the concrete.
Table 1: Recommended Mix Proportions for Different Grades of Concrete
Grade of Concrete | Cement (kg/m3) | Fine Aggregate (kg/m3) | Coarse Aggregate (kg/m3) | Water (kg/m3) |
---|---|---|---|---|
M5 | 250 | 190 | ||
M10 | 220 | 560 | 180 | |
M15 | 205 | 515 | 175 | |
M20 | 190 | 480 | 975 | 170 |
M25 | 185 | 450 | 882 | 165 |
Note that these proportions are indicative and may vary based on the specific requirements of the project and the materials used. It is critical to test the mix proportions through trial mixes before adopting them for a construction project.
Size of Aggregates
The size of aggregates is a crucial factor affecting the workability of concrete. Smaller aggregates are preferred over larger aggregates since they provide better workability due to increased surface area. On the other hand, larger aggregates can make the mix less cohesive and challenging to work with.
So, choosing the right size of aggregates according to the desired workability and placement requirements is paramount. Concrete professionals must also consider the availability of aggregates and the characteristics of the materials used in the mix.
For example, Blue Metal Jelly is a popular type of aggregate that is used primarily in construction projects. The size of blue metal jelly ranges from 4 mm to 20 mm, making it suitable for a variety of concrete mixes.
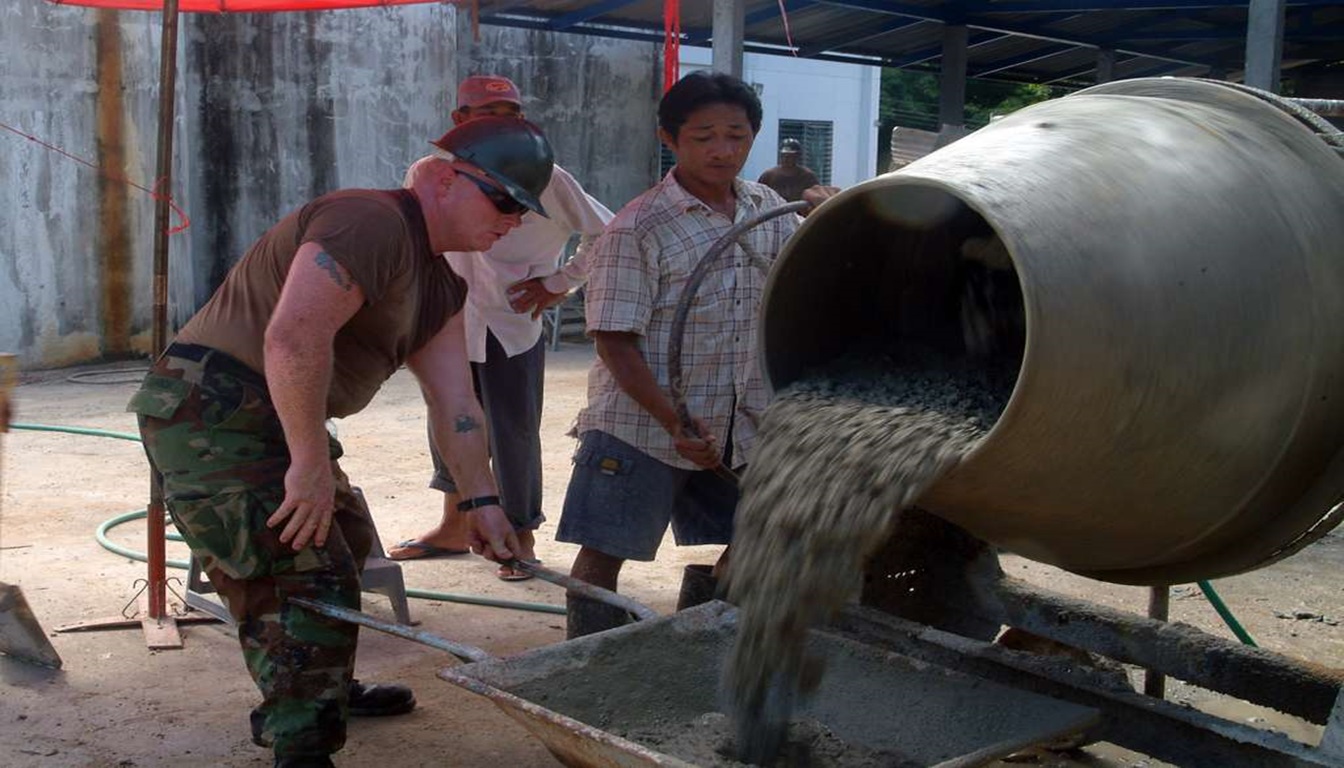
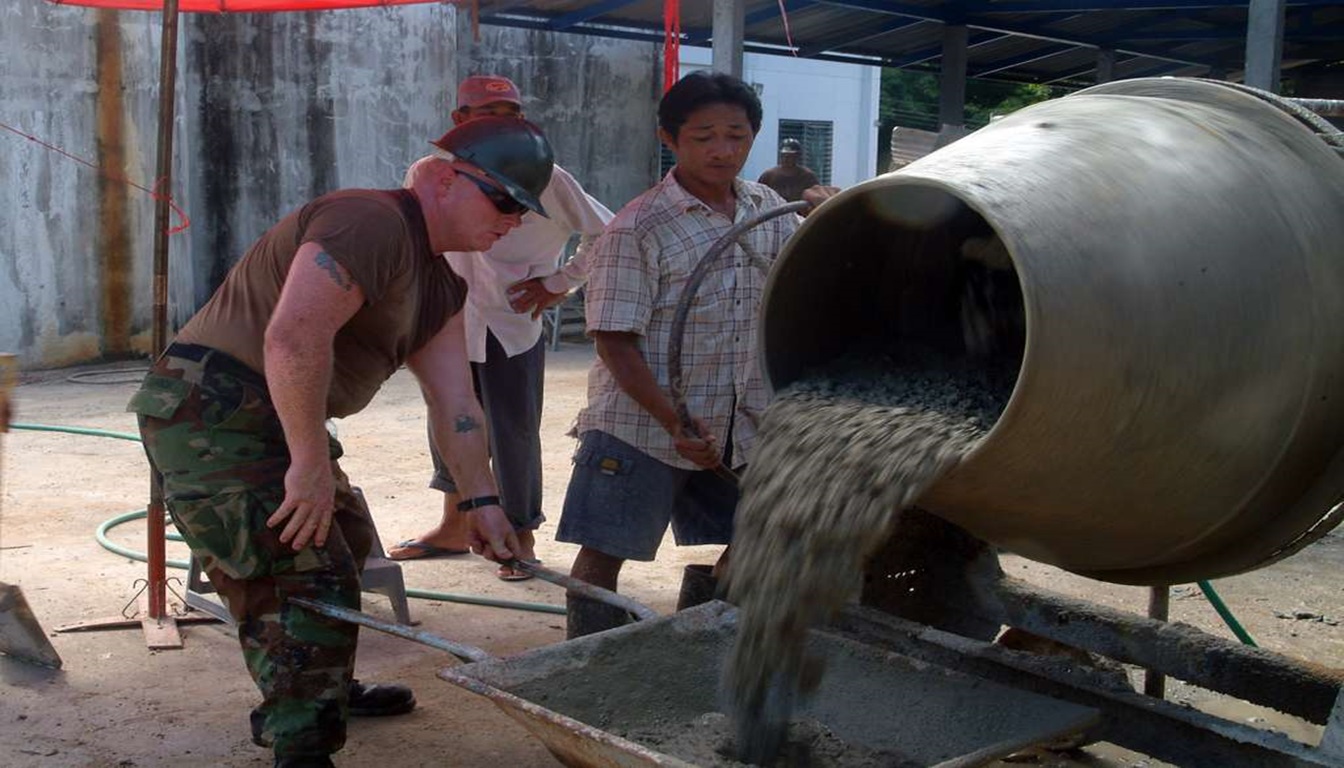
Comparison of workability of concrete with different aggregate sizes
Aggregate size | Workability |
---|---|
Less than 5 mm | Excellent |
5-10 mm | Good to excellent |
10-20 mm | Fair to good |
Above 20 mm | Poor |
The table above shows a comparison of the workability of concrete with different aggregate sizes. It highlights the importance of selecting the right size of aggregates to achieve the desired workability in concrete mixes.
Shape of Aggregates
When it comes to the workability of concrete, the shape of aggregates plays an important role.
Aggregates with irregular shapes tend to interlock, making the mix less workable, while rounded and smooth aggregates can enhance workability. Therefore, careful consideration of the shape of aggregates is essential in optimizing concrete workability.
An easy way to visualize how different shapes of aggregates can affect workability is through the following table:
Shape of Aggregates | Effect on Workability |
---|---|
Irregular | Interlock, reduce workability |
Rounded and smooth | Enhance workability |
Note: The workability of Concrete can be enhanced by using rounded aggregates instead of irregularly shaped ones.
By choosing the appropriate shape for aggregates, construction professionals can ensure that the mix is optimally workable, making it easier to place the concrete where required.
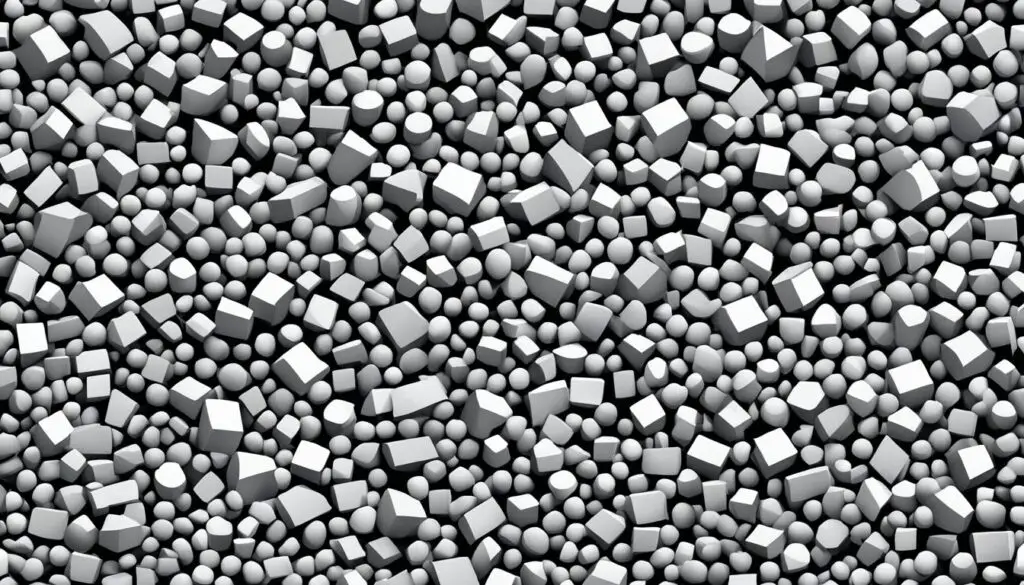
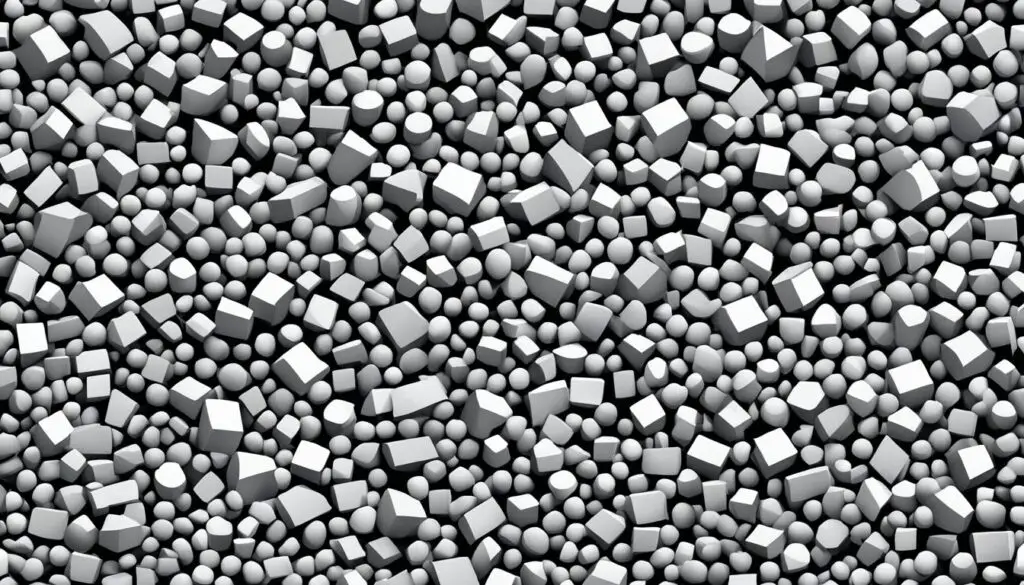
Grading of Aggregates
The grading, or particle size distribution, of aggregates is one of the critical factors that affect the workability of concrete. A well-graded mix with a range of particle sizes provides better workability compared to a poorly graded mix. A well-graded mix reduces the void content and ensures better lubrication between aggregate particles. This leads to increased flowability and ease of placement of the concrete mix.
Grading | Description | Effects on Workability |
---|---|---|
Well-graded | A mix containing different sizes of aggregates in the required proportions | Produces a more workable mix and reduces the amount of cement paste needed |
Poorly graded | A mix containing only one size of aggregate or poorly distributed aggregate sizes | Produces a less workable mix and increases the amount of cement paste needed |
Properly grading the aggregates is necessary to achieve the desired workability of the concrete mix. The use of well-graded aggregates reduces the need for excessive cement, resulting in a more sustainable and cost-effective solution.
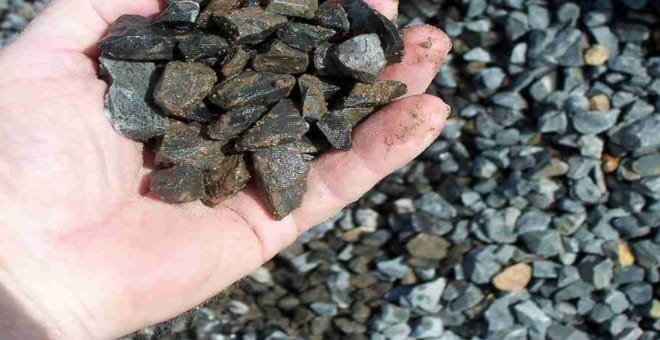
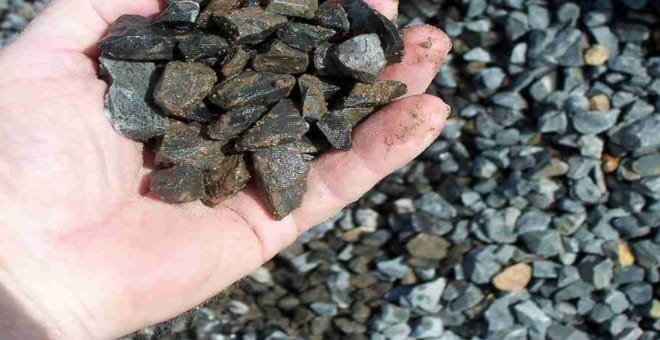
Next, we’ll explore the surface texture of aggregates and its impact on the workability of concrete.
Surface Texture of Aggregates
The surface texture of aggregates is another crucial factor that affects the workability of concrete. Smooth aggregates tend to reduce friction, which improves flow and enhances workability. On the other hand, rough-textured aggregates can result in a mix with reduced workability. Therefore, selecting aggregates with the appropriate surface texture is crucial.
For example, if the surface texture of the aggregates is too rough, it can cause increased interlocking of particles, making it difficult for the mix to flow. The image below shows the impact of surface texture on the workability of concrete:
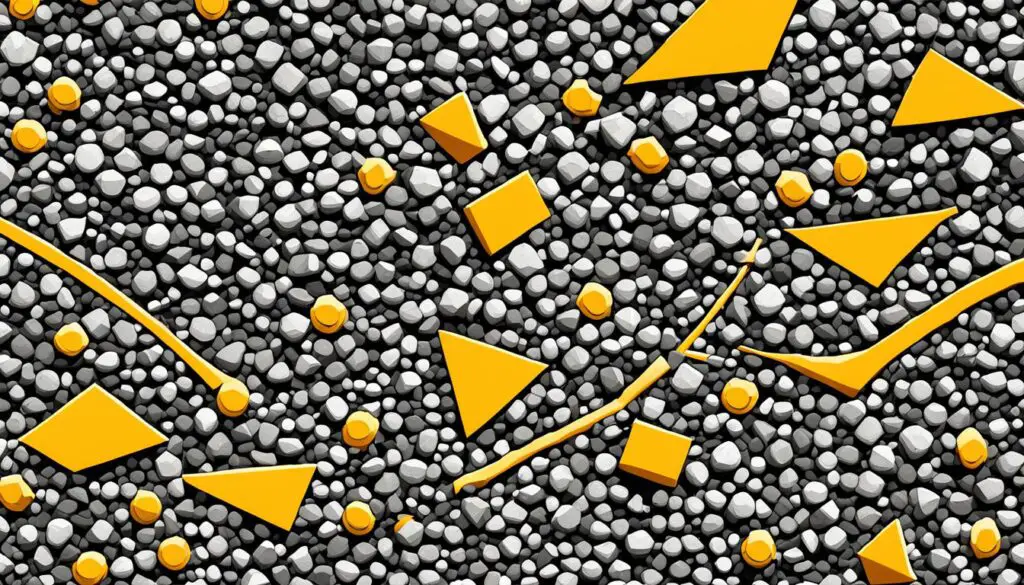
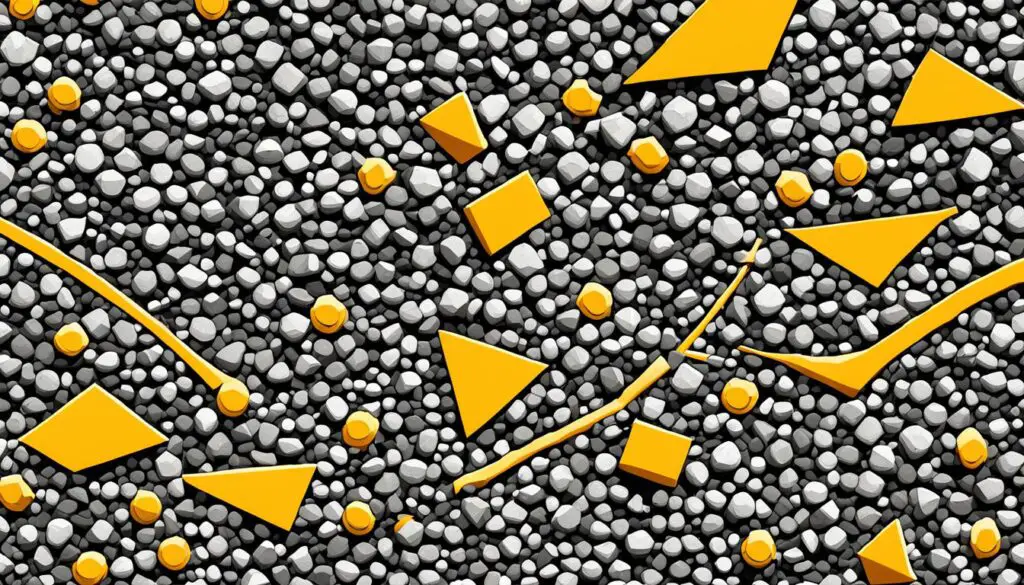
As you can see from the image, smooth aggregates have better flowability than rough-textured aggregates. Therefore, it is essential to choose aggregates based on the required surface texture to ensure the optimal workability of concrete mixes.
Use of Admixtures
Admixtures are chemical additives used to modify the properties of concrete mix. They can significantly impact the workability of concrete, making it easier to place and reducing the need for additional water. The use of admixtures is a common practice in modern concrete construction, where construction professionals aim to optimize workability while achieving the required strength and durability.
Two prominent types of admixtures are plasticizers and superplasticizers. Plasticizers are used to increase the workability of concrete, reducing the water-cement ratio and enhancing the ease of placement. Superplasticizers, on the other hand, provide even higher levels of workability, enabling the placement of concrete with varying levels of slumps, while still maintaining its stability and strength.
However, it is vital to understand the appropriate use of admixtures, as excessive use can have adverse effects on the strength and durability of the mix. Additionally, the right type and dosage of admixture must be chosen based on the mix’s specific requirements and other factors affecting workability, such as temperature and aggregate properties.
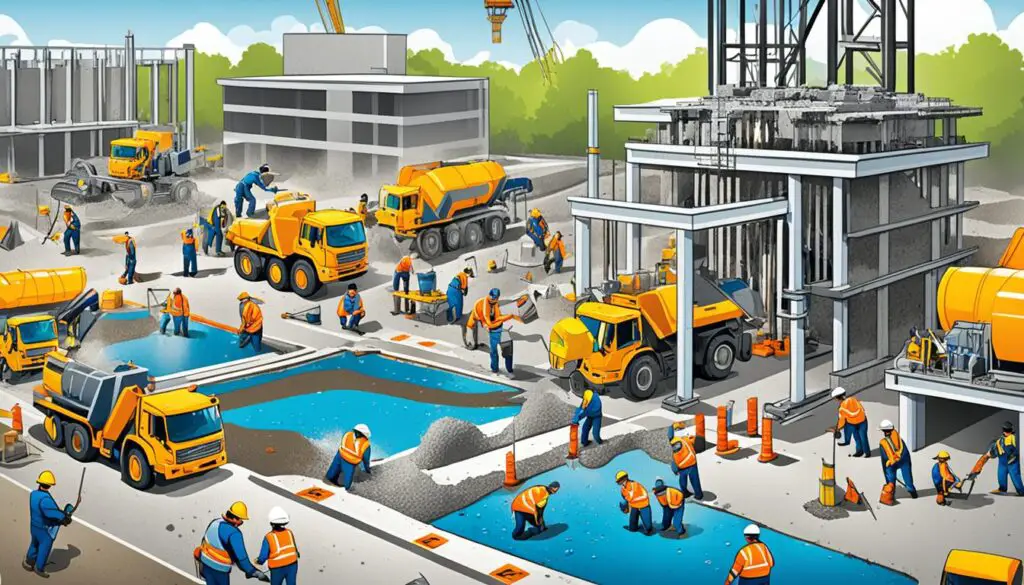
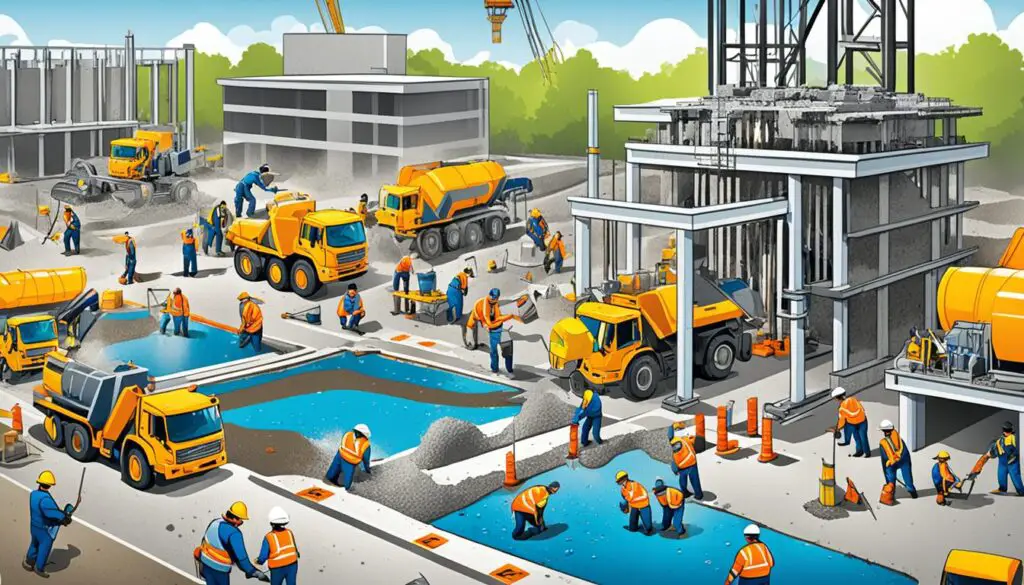
Proper use of admixtures can significantly impact the workability of concrete, minimize costs during construction and waste of cement, and help achieve the desired mix characteristics. Construction professionals must have a thorough understanding of the appropriate use of admixtures to ensure the optimal workability of the mix and the successful completion of construction projects.
Use of Supplementary Cementitious Materials
Supplementary cementitious materials play a vital role in influencing the workability of concrete. Fly ash and silica fume are two commonly used materials that can enhance the workability of a mix. The microspheres in fly ash reduce surface tension, resulting in a more workable mix, while silica fume particles decrease the distance between individual cement grains, thus improving cohesion and reducing the risk of bleeding. By utilizing supplementary cementitious materials in concrete design and using appropriate proportions, the workability and durability of the mix can be significantly improved.
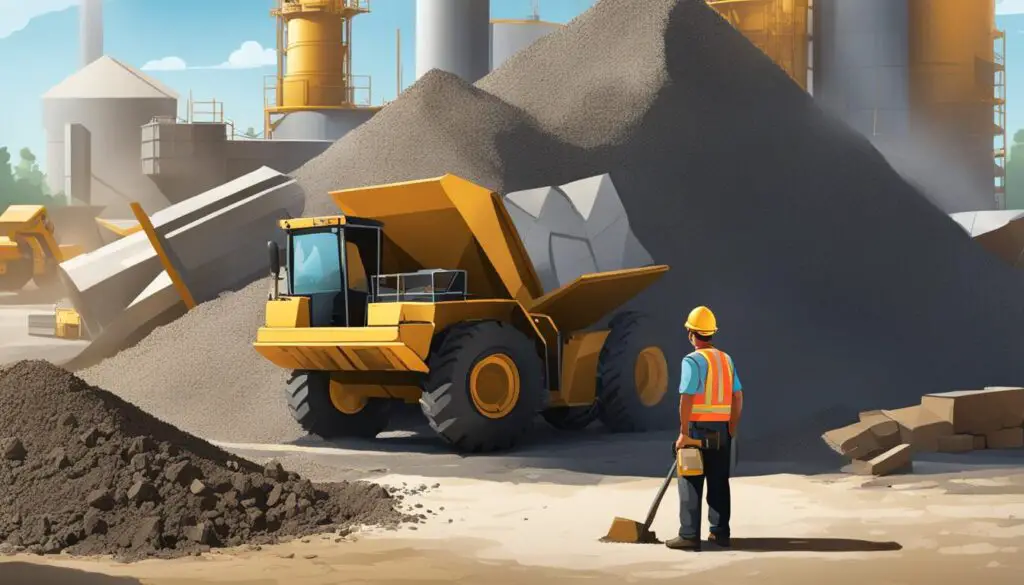
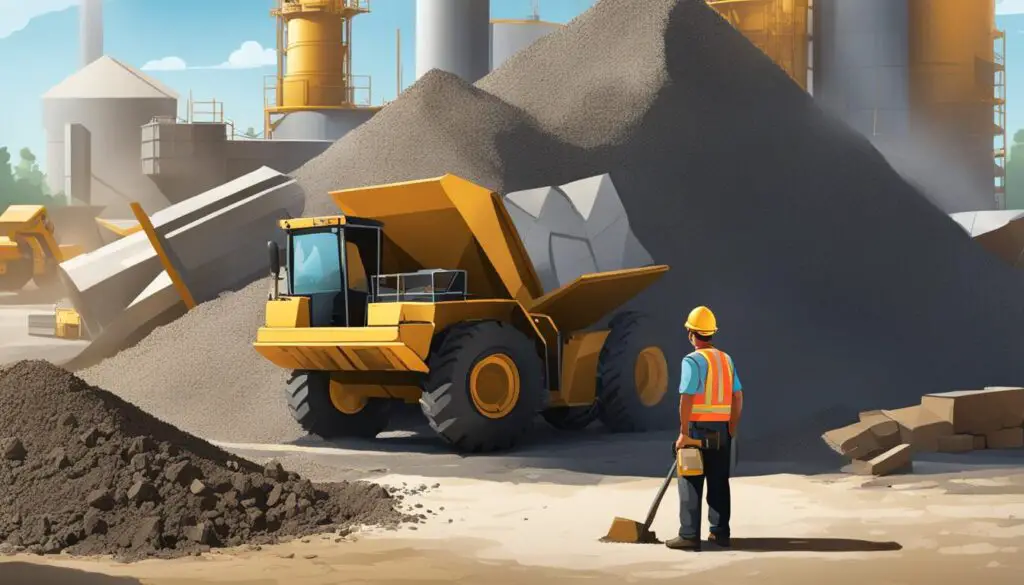
Table: Comparison of Workability of Concrete Mixes with and without Supplementary Cementitious Materials
Concrete Mixes | Workability (Slump Value) |
---|---|
Without Supplementary Cementitious Materials | 50 mm |
With Fly Ash | 80 mm |
With Silica Fume | 100 mm |
From the table, it is clear that the incorporation of supplementary cementitious materials significantly improves the workability of concrete mixes. This reinforces the importance of utilizing these materials in the design of concrete mixes for construction projects where workability is a primary concern.
Time
The time elapsed since the mix was prepared is an essential factor that can affect the workability of concrete. Over time, the water in the mix is absorbed by the aggregates, leading to reduced workability due to hydration and setting. It is crucial to plan and monitor the time between mixing and placing the concrete to ensure that workability is maintained throughout the construction process.
Concrete with high workability is easier to place, compact, and finish, resulting in a smoother and more durable surface. Hot weather conditions can speed up hydration, reducing workability, while low-temperature conditions can delay hydration, leading to improved workability but also potential strength issues.
Proper planning for transportation, pouring, and finishing can help maintain the right workability for a more extended period. When faced with unforeseen delays, adding water to the mix should be avoided as it adversely affects the strength of the concrete. Instead, using a plasticizer or superplasticizer can help increase the workability of the mix without affecting the strength.
How does time affect workability?
The longer the time elapsed since mixing the concrete, the lower the workability. After mixing, the concrete has a certain amount of free and absorbed water available for hydration and setting. Over time, the free water is absorbed by the aggregates, reducing the amount of workable water in the mix. This results in a stiffer, drier mix with lower flowability and ease of placement. Additionally, delayed placement of the concrete beyond the initial set time can lead to segregation, bleeding, and cracking, affecting the workability.
How is time managed during construction?
Various factors can impact the time between mixing and placing the concrete, including transportation time, temperature, and placement method. Proper planning and monitoring can help ensure that the concrete maintains the desired workability during construction. This includes setting realistic schedules, considering weather forecasts, and monitoring the time elapsed since mixing. Admixtures, such as retarders, can also be added to the mix to delay hydration and extend workability.
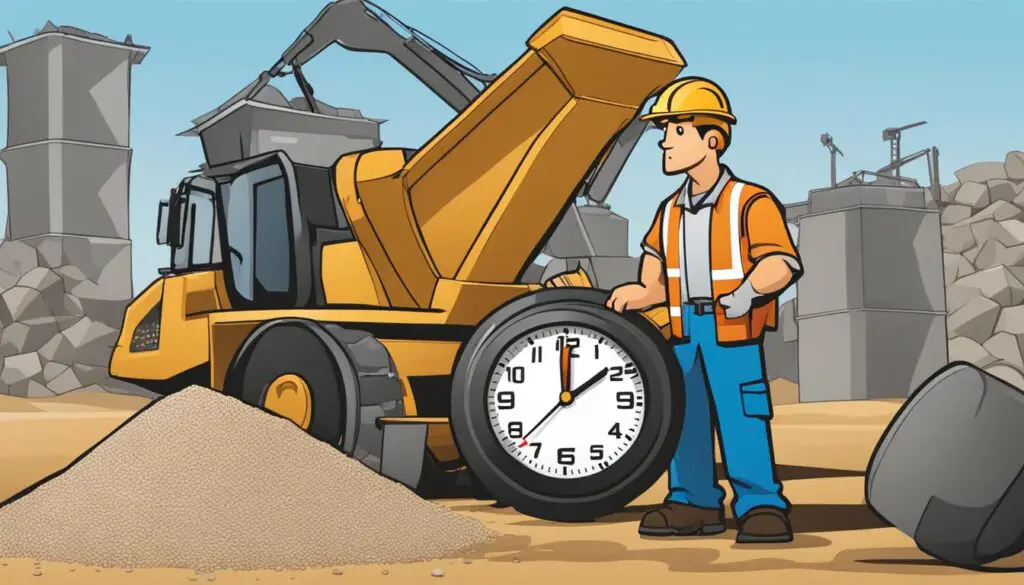
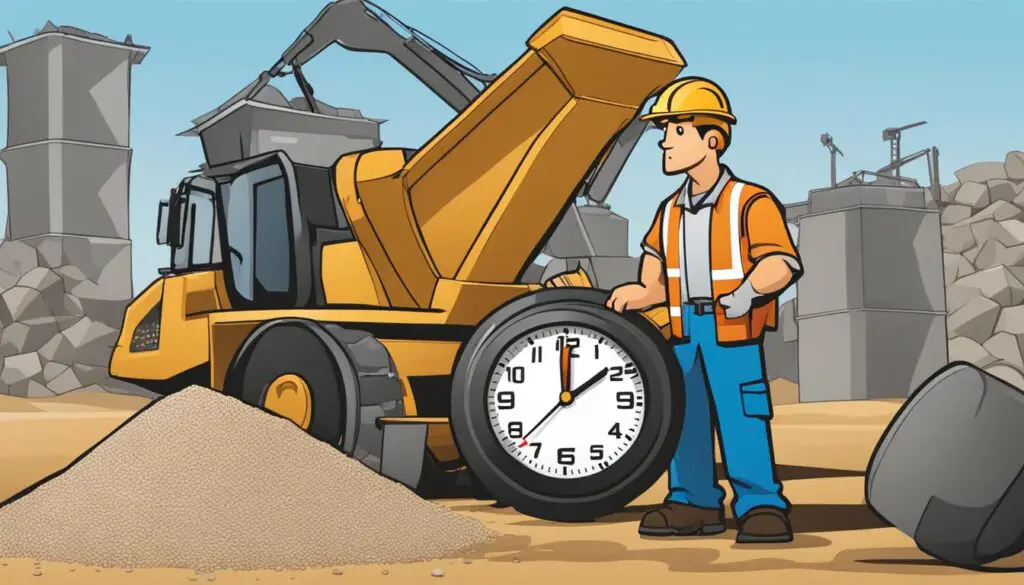
Temperature
The temperature of the concrete mix is a critical factor that impacts its workability. Higher temperatures can affect the setting time of concrete, leading to reduced workability and slump loss. On the other hand, lower temperatures can delay the setting time and increase workability for a more extended period. Therefore, it is essential to consider the environmental temperature when mixing and placing concrete.
Moreover, hot weather can lead to rapid evaporation of the mixing water, making the concrete surface dry and prone to cracking. One way to address this issue is to keep the concrete surface moist by sprinkling water before and after placing the concrete. Additionally, using cold mixing water or ice can help lower the concrete temperature and extend workability.
In colder regions, it is crucial to ensure that the concrete mix does not freeze during the winter months. Using heated aggregates or mixing water can prevent the concrete mix from freezing and ensure proper setting and hardening.
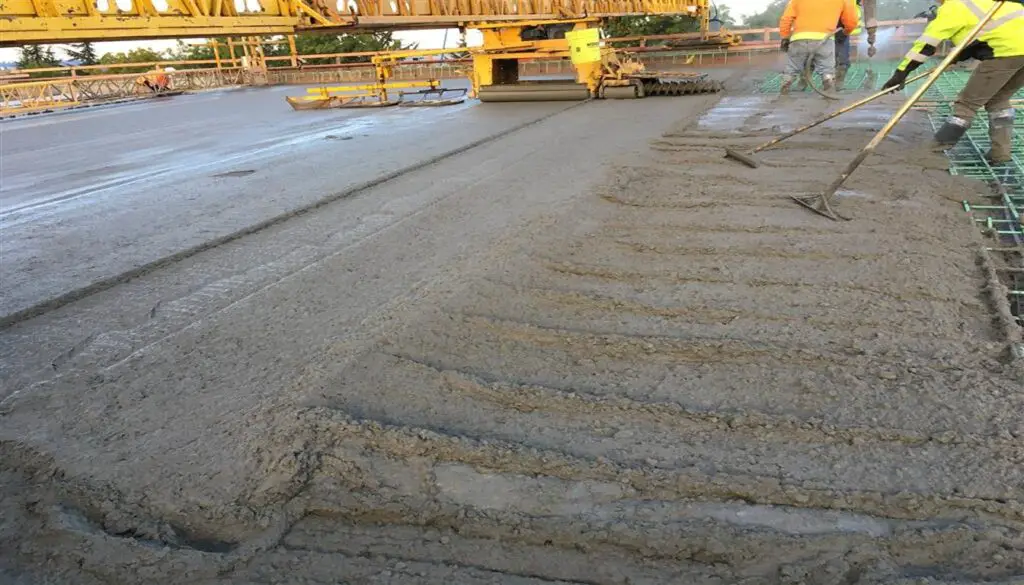
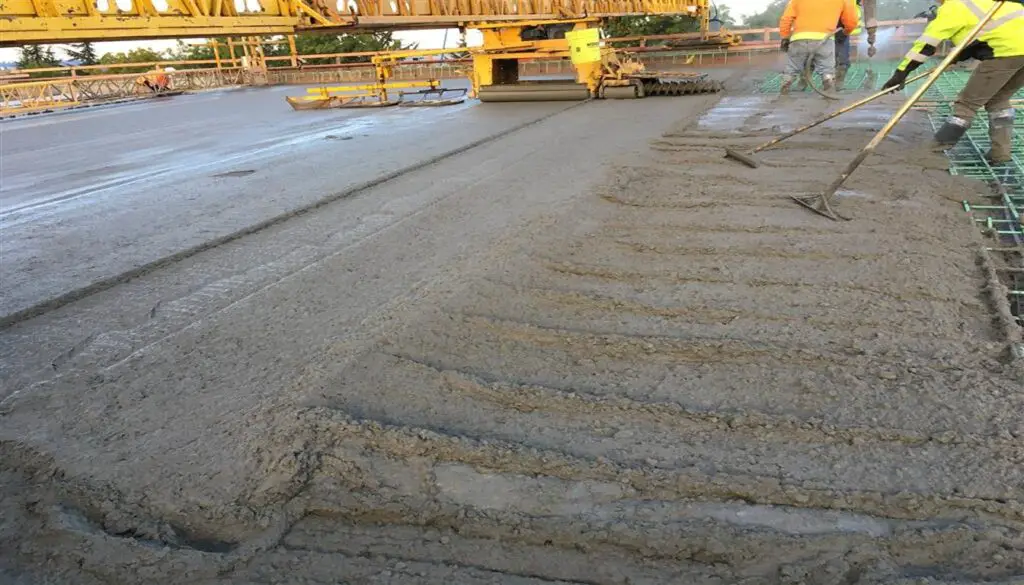
In conclusion, understanding the impact of temperature on the workability of concrete is necessary for optimizing concrete mixes in construction projects. Factors such as high temperatures and cold weather can affect the setting time and workability of concrete. Therefore, it is essential to take appropriate measures to ensure the concrete mix reaches the desired workability and strength level.
Conclusion
In conclusion, workability is a crucial factor in achieving successful construction projects using concrete. The factors that affect workability include water content, mix proportions, aggregate size and shape, grading, surface texture, use of admixtures, use of supplementary cementitious materials, time, and temperature. By understanding and controlling these factors, construction professionals can optimize concrete mixes and placement to achieve the desired workability. This results in cost savings, improved efficiency, and durable structures that meet or exceed project requirements.
Therefore, engineers, contractors, and project managers need to collaborate and plan carefully to ensure that all factors affecting workability are addressed before and during construction. By doing so, they can minimize the risks of issues such as weak concrete, cracking, and poor durability.
Overall, improving workability in concrete is a continuous process that requires careful attention to detail and a commitment to quality. By prioritizing workability and following these essential factors affecting it, construction professionals can ensure the successful and efficient completion of concrete projects.
Thanks For the Great Attention!
Good Bye & Take Care
Happy Learning
Also, Read,