High Alumina Cement (HAC) is a popular construction material known for its exceptional strength and durability. It is widely used in specialized projects where ordinary Portland cement (OPC) may not be suitable, such as in marine structures or precast components. In this section, we will provide a comprehensive overview of HAC, including its uses, properties, advantages, disadvantages, and chemical composition, as specified by IS code 6452-1989.
Key Takeaways:
- High Alumina Cement (HAC) is a specialized construction material that offers exceptional strength and durability.
- HAC is suitable for specific applications such as in precast components or marine structures, where OPC may not be suitable.
- HAC has unique properties that make it ideal for specialized applications but it also has potential drawbacks that need to be considered before use.
- The chemical composition of HAC is specified by the IS code 6452-1989.
- Understanding the properties and applications of HAC can help engineers and builders make informed decisions about its use in construction projects.
Application and Uses of High Alumina Cement
HAC finds its application in various construction projects. Due to its unique properties, it is commonly used in projects that require high strength and durability. Its excellent resistance to chemical attacks makes it a suitable choice for building structures that will be exposed to harsh chemical environments.
One of the primary uses of HAC is in the construction of refractory linings for industrial furnaces, kilns, and incinerators. Its superior performance in high-temperature environments makes it an ideal choice for such applications.
It is also used in the production of precast components such as precast concrete pipes, blocks, and panels. Compared to other types of cement, it offers faster curing times, enabling quicker production times and turnaround.
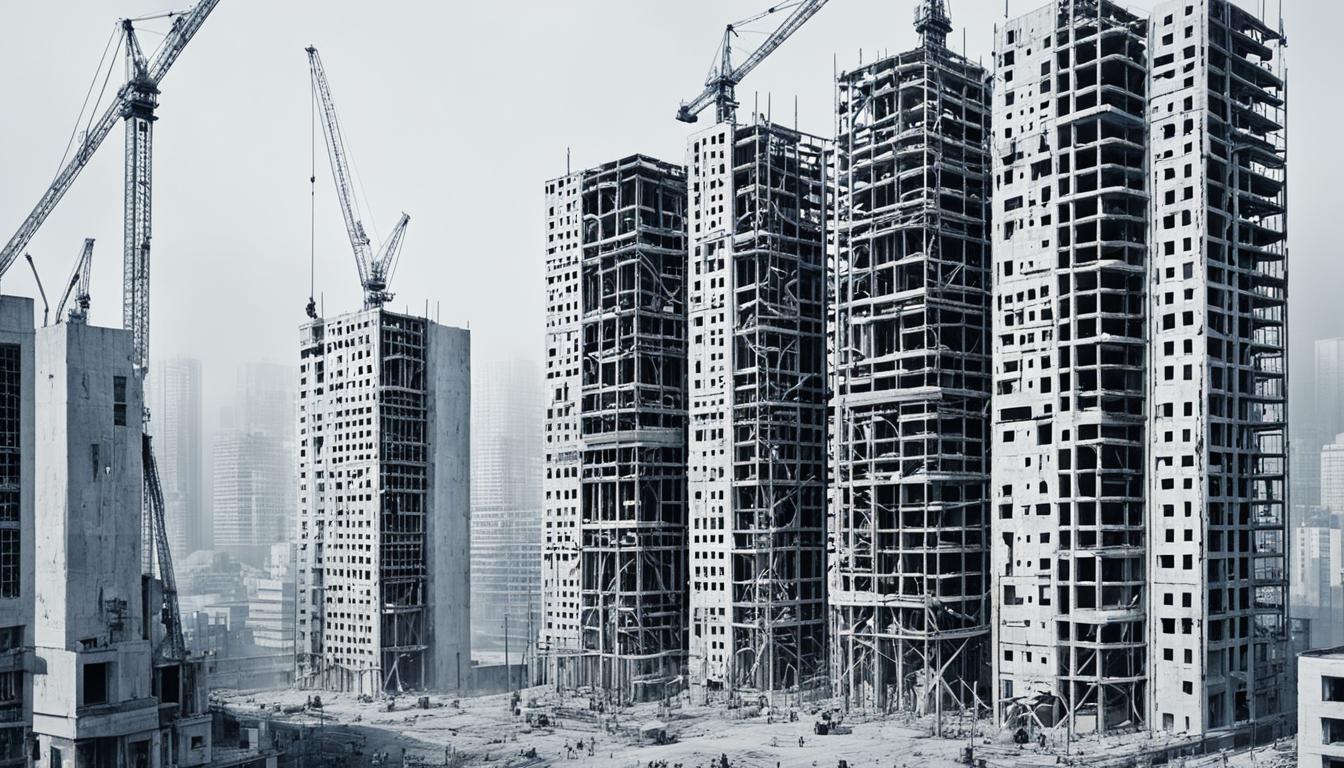
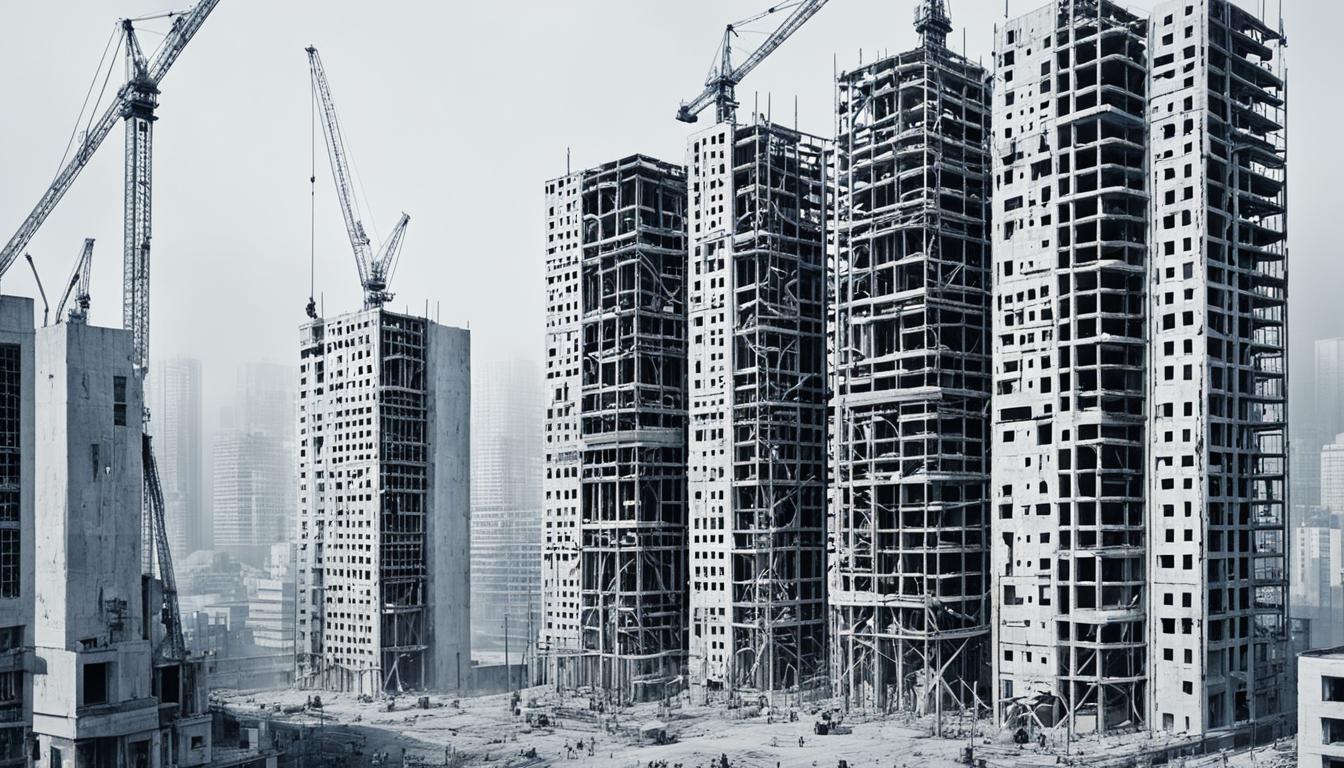
Another significant application of HAC is in the construction of marine structures. Its ability to resist seawater corrosion and sulfate attacks makes it an ideal choice for projects such as seawalls, dockyards, and harbors.
In summary, HACt is a versatile construction material that finds numerous applications in specialized projects that require superior strength, durability, and chemical resistance.
Advantages of High Alumina Cement
When it comes to modern construction projects, HAC offers numerous advantages over ordinary Portland cement. Below, we’ve highlighted some of the key benefits that make HAC a popular choice for a variety of specialized applications.
Exceptional Strength and Durability
One of the most significant advantages of HAC is its exceptional strength and durability. With compressive strengths ranging from 40 to 70 MPa, high alumina cement can withstand heavy loads and resist deformation and cracking, making it an ideal choice for the construction of high-rise buildings, bridges, and other critical infrastructure.
Resistance to Chemical Attacks
Another notable advantage of HAC is its outstanding resistance to chemical attacks, especially from sulfate and acid-based compounds. This makes it the go-to choice for constructing industrial chimneys, exhaust stacks, and other structures that are exposed to high levels of chemical pollutants and harsh weather conditions.
Reduced Setting Time
Compared to ordinary Portland cement, HAC has relatively shorter setting times, allowing for faster construction and reduced labor costs. This feature is particularly critical in regions with extreme weather conditions, where longer setting times can prolong curing periods, leading to delays and higher expenses.
Less Vulnerable to Cracking
HAC is less vulnerable to cracking and shrinkage compared to ordinary Portland cement, thanks to its low heat generation properties and minimal hydration expansion. This quality makes it an ideal choice for the construction of pre-stressed concrete components, where cracking can lead to structural failure and reduced safety.
Resistant to High Temperatures
HAC is highly resistant to high temperatures, making it the material of choice for the construction of furnaces, ovens, and other heat-based applications. This is because HAC can withstand temperatures of up to 1600°C without degrading, ensuring optimal performance and long-term cost savings.
Considering its exceptional strength, durability, and resistance to chemical attacks, it’s no wonder that HAC is a popular choice for specialized construction applications.
Disadvantages of High Alumina Cement
While high alumina cement offers unique properties and advantages, it also has some potential drawbacks and limitations. It is essential to consider these disadvantages before opting for HAC in construction projects.
One major disadvantage of HAC is its high cost compared to ordinary Portland cement. Its production requires specialized manufacturing processes and high-quality raw materials, which can drive up the overall cost of the cement.
Another concern is its shorter setting time, which requires immediate processing and handling after mixing with water. Any delay can lead to a rapid hardening of the cement mixture, making it difficult to use and compromising its effectiveness.
The need for proper curing techniques is also crucial for preventing shrinkage in HAC. Without adequate curing, it may experience volume changes, resulting in cracks and weakened structural integrity.
To avoid these drawbacks, it is crucial to understand the properties and requirements of high alumina cement fully. Additionally, careful handling, processing, and curing practices can optimize its performance while minimizing any potential disadvantages.
Chemical Composition of High Alumina Cement
In this section, we will provide detailed insights into the chemical composition of HAC, as per the IS code 6452-1989. The cement is composed mainly of calcium aluminate and a small amount of other compounds, which play a crucial role in its unique properties.
The main chemical components of HAC are:
Compound | Chemical Formula | Percentage by Weight (%) |
---|---|---|
Calcium mono-aluminate | CaO.Al2O3 | CaO is around 35% – 50%, and Al2O3 content ranges between 47% – 65% |
Dicalcium aluminate | CaO.2Al2O3 | 5% – 10% |
Tricalcium aluminate | CaO.3Al2O3 | 6% – 10% |
Tetracalcium trialuminate | 4CaO.Al2O3 | 2% – 8% |
The chemical composition of high alumina cement plays a significant role in determining its properties, such as high early strength, low heat of hydration, and exceptional resistance to sulfate attacks, among others. Calcium mono-aluminate is the main source of early strength, while dicalcium aluminate contributes to the setting and hardening process. Tricalcium aluminate and tetra calcium tri aluminate provide later strength gain and improved durability. A well-adjusted chemical composition may also improve the refractory properties of the cement, making it suitable for high-temperature applications.
Understanding the chemical composition of HAC is crucial for engineers and builders to choose the right type of cement for specialized construction projects.
High Alumina Cement Properties
HAC stands out from other Portland cement due to its unique properties. Its superior early strength is attributed to its higher percentage of alumina, in contrast to the traditional Portland cement that depends on limestone. HAC releases less heat during the hydration process, preventing thermal stress that could occur during large-scale construction projects.
HAC also maintains its mechanical strength, even when exposed to high temperatures, making it an ideal choice for refractory applications such as furnace linings and kiln construction. HAC exhibits a high resistance to sulfate attacks, which is critical for the construction of marine structures and underground projects.
Property | Description |
---|---|
Early Strength | HAC exhibits exceptional strength, even in the early stages of curing, making it ideal for time-critical projects. |
Heat of Hydration | The heat released during the hydration process is lower than that of Portland cement, minimizing the risk of thermal cracking. |
Sulfate Resistance | HAC’s improved resistance against sulfate attacks ensures its durability in harsh environments. |
Refractory Properties | HAC’s high-temperature resistance makes it a popular choice for refractory applications. |
With its unique properties and superior performance, high alumina cement is suitable for specialized construction projects that demand exceptional strength, durability, and resistance to harsh environmental factors.
Comparison between High Alumina Cement and Ordinary Portland Cement
HAC and ordinary Portland cement (OPC) are two widely used types of cement in the construction industry. While both serve the same purpose of binding material, they have their unique properties that set them apart from each other. In this section, we will compare HAC and OPC based on their strength, durability, setting time, and cost to provide a comprehensive analysis of the two cement types.
High Alumina Cement (HAC) | Ordinary Portland Cement (OPC) | |
---|---|---|
Main Constituents | Calcium aluminate compounds Calcium oxide Silica |
Tricalcium Silicate Dicalcium Silicate Tricalcium Aluminate Tetracalcium Aluminoferrite |
Strength | HAC has exceptional early strength, making it ideal for precast components and rapid repairs. | OPC has a slower strength development but yields a higher ultimate compressive strength and is more commonly used for structural purposes. |
Durability | HAC offers excellent resistance to chemical attacks and high temperatures, making it ideal for refractory applications. | OPC is susceptible to chemical attacks and has lower resistance to high temperatures. |
Setting Time | HAC has a shorter setting time than OPC but requires proper curing techniques to prevent shrinkage. | OPC has a longer setting time but allows for more extended workability. |
Cost | HAC is generally more expensive than OPC. | OPC is more economical and widely available. |
Overall, the choice between HAC and OPC depends on the specific project requirements. While HAC offers unique properties that make it suitable for specialized applications, OPC remains the most commonly used type of cement. A cost-benefit analysis is essential to make an informed decision regarding the selection of the appropriate cement type for a particular project.
IS Code for High Alumina Cement
High alumina cement is regulated by a specific set of standards, guidelines, and specifications set by the Indian Standards Institute (ISI). The IS code for HAC is 6452-1989, which provides detailed instructions on the production process, testing methods, and permissible limits for various physical and chemical properties.
It covers aspects such as the chemical composition, setting time, compressive strength, and sulfate resistance. Any manufacturer or supplier of HAC must meet the requirements laid out in this code to ensure the product’s quality and reliability.
Why is the IS code for high alumina cement important?
The IS code for high alumina cement is essential as it guarantees the consistent quality of the product, ensuring its safety and performance. It also helps in standardizing the testing and approval processes, making it easier for builders, engineers, and regulators to assess the suitability of HAC for different applications.
What are the key highlights of the IS code for high alumina cement?
ASPECT | HIGHLIGHTS |
---|---|
Chemical composition | Limits on the content of various oxides, including Al2O3, SiO2, Fe2O3, CaO, MgO, and SO3 |
Setting time | Not less than 30 minutes and not more than 600 minutes |
Compressive strength | Minimum 40 MPa after 3 days and 70 MPa after 7 days |
Sulfate resistance | Not less than 80% of the strength retention after immersion in 14% sodium sulfate solution for 6 months |
The IS code for high alumina cement also specifies the packaging, labeling, and storage requirements to ensure the safety and integrity of the product. It is essential to adhere to these guidelines to avoid any damage, contamination, or degradation of HAC.
Initial Setting Time of High Alumina Cement
As we know, the setting time of cement refers to the time taken by cement to set, implying the loss of plasticity in concrete. Initial setting time is the time taken by cement to partially lose its plasticity after adding the mixing water. The initial setting time of HAC is typically shorter than that of ordinary Portland cement due to its unique chemical composition.
The initial setting time of high alumina cement can depend on several factors, including the ambient temperature, relative humidity, water-to-cement ratio, and chemical admixtures. Higher temperatures and lower moisture levels can speed up the setting process, while lower temperatures and higher moisture levels can slow it down.
It is imperative to follow proper handling and curing techniques while working with HAC to ensure optimal performance. Proper mixing of high alumina cement with water, adequate placement, and correct finishing techniques can help control the initial setting time and prevent shrinkage cracks. Adequate curing is necessary to maintain the required moisture levels for optimal strength development.
The initial setting time of high alumina cement is crucial to ensure the stability and longevity of the construction project. Understanding the factors that affect the initial setting time can help builders and engineers make informed decisions to optimize the performance of HAC for their specific application.
Applications of High Alumina Cement in Construction
HAC’s unique properties make it an outstanding choice for specialized construction projects. Let’s explore some of its applications:
Refractory linings
High alumina cement is widely used in the construction of refractory linings for furnaces, kilns, and other high-temperature applications. Its exceptional strength, resistance to thermal shock, and low porosity make it an ideal choice for ensuring the longevity and reliability of refractory structures.
Precast components
High alumina cement is used in the manufacture of precast concrete components, including pipes, tiles, and slabs. Its high early strength and durability ensure that the components have a long service life and can withstand the harsh conditions of their intended use.
Marine structures
High alumina cement is commonly used in the construction of marine structures, such as sea walls, jetties, and piers. Its excellent resistance to sulfate attacks and corrosion makes it an optimal choice for ensuring the structures’ longevity in the harsh marine environment.
Other specialized applications
HAC’s exceptional properties make it an ideal choice for other specialized construction projects, including industrial floors, underground structures, and repair works. Its suitability for these applications stems from its high early strength, low heat of hydration, and excellent chemical resistance.
Environmental Impact of High Alumina Cement
As we continue to push for a more sustainable future, it’s necessary to consider the environmental impact of high alumina cement. One of the main concerns is its high energy consumption and consequent CO2 emissions during the production process. Research shows that the carbon footprint of HAC is almost double that of ordinary Portland cement, which is already a significant contributor to greenhouse gas emissions.
Another factor to consider is the sourcing of raw materials. The production of high alumina cement requires bauxite, which is a non-renewable resource. The mining process can cause land and environmental degradation, impacting surrounding ecosystems and communities.
Despite these concerns, some steps can be taken to mitigate the environmental impact of HAC. One approach is to reduce energy consumption during the production process by optimizing kiln design and using alternative fuels. Additionally, the use of recycled materials and optimizing end-of-life processing can help reduce the environmental footprint.
Builders and engineers must consider the ecological impact of high alumina cement when making material choices. By utilizing sustainable production methods and exploring alternative materials, we can work towards reducing our environmental impact and creating a more sustainable future.
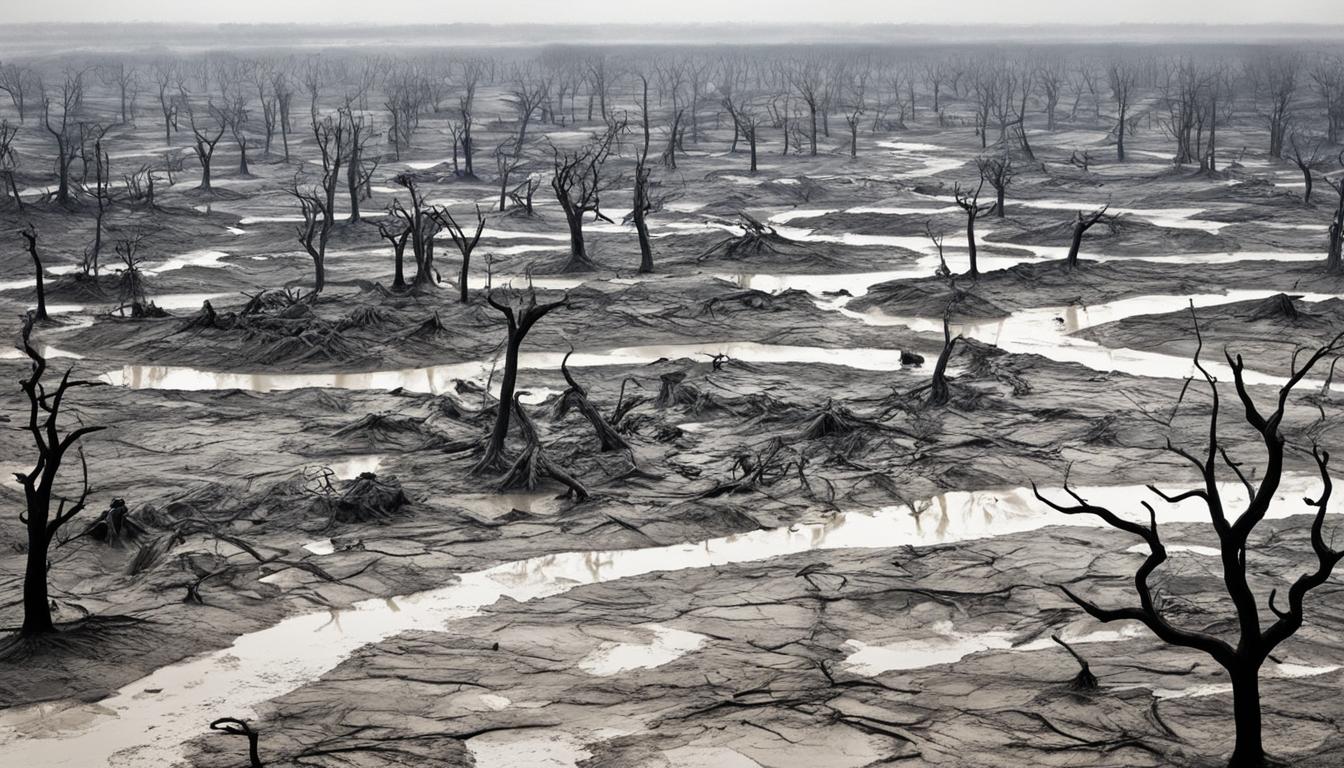
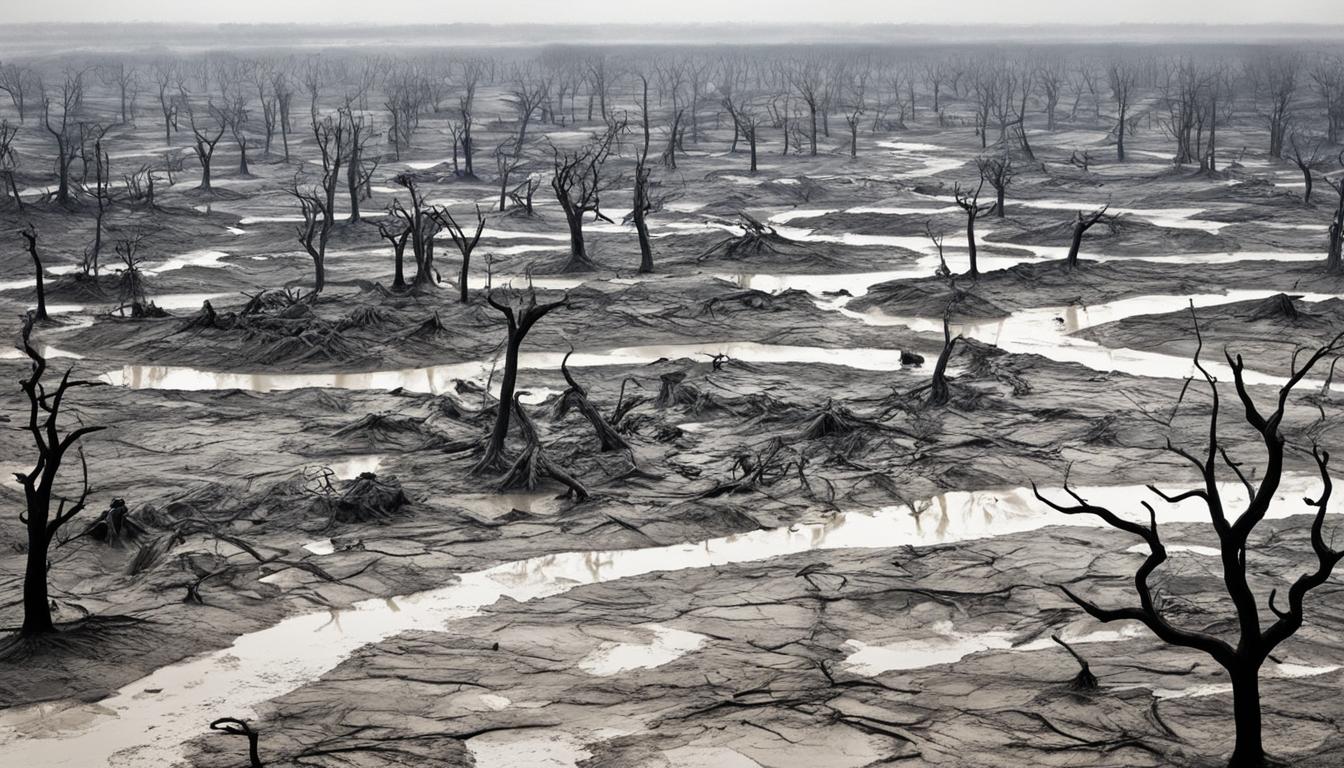
Common FAQs About High Alumina Cement
High alumina cement is increasingly gaining popularity in the construction industry due to its exceptional strength, durability, and resistance to chemical attacks. As a result, builders and engineers have understandably been curious about its properties, usage, and handling. In this section, we answer some of the most common questions about HAC.
1. Is high alumina cement compatible with other materials?
Yes, high alumina cement can be used in conjunction with other materials, including regular Portland cement, aggregates, and admixtures. However, it is essential to consider the compatibility of the materials to avoid any adverse chemical reactions between them during construction.
2. Are there any special storage and handling precautions for high alumina cement?
High alumina cement should be stored in dry and well-ventilated areas to prevent moisture absorption or contamination. It is also essential to wear suitable protective gear, including gloves and goggles when handling HAC to avoid contact with eyes and skin and potential inhalation of dust particles.
3. Is high alumina cement more expensive than regular Portland cement?
Yes, HAC is relatively more expensive than regular Portland cement due to its specialized production process and unique properties. However, it is worth the investment for projects that require exceptional strength durability, and protection against chemical attacks.
4. Can high alumina cement be used in precast components?
Yes, high alumina cement is an ideal choice for precast components such as refractory monolithic components, precast blocks for industrial furnace linings, pipes, and castables for the iron and steel industries.
5. Are there any potential alternatives to high alumina cement?
Yes, there are alternative construction materials available, including ordinary Portland cement, calcium aluminate cement, and geopolymer cement. However, each of these materials has its specific properties, advantages, and drawbacks, and it is essential to evaluate them based on the project requirements before deciding on the best option.
Case Studies: Successful Applications of High Alumina Cement
HAC has been widely used in construction projects that require exceptional strength, durability, and resistance to chemical attacks. In this section, we will showcase real-world case studies of successful applications of HAC to illustrate its unique properties and advantages over ordinary Portland cement.
Case Study 1: Marina Bay Sands, Singapore
Marina Bay Sands is an iconic integrated resort located in Singapore, consisting of three 55-story towers joined at the top by a sky park. The project used over 7,000 cubic meters of high-performance concrete, including HAC, for its structural foundation.
“The use of high alumina cement was critical in achieving the desired strength, durability, and shrinkage control for the elevated structures of Marina Bay Sands. Additionally, HAC improved the workability and sulfuric acid resistance, which are particularly essential for constructions near water,” says the lead engineer.
Case Study 2: Varso Tower, Warsaw
Varso Tower is a skyscraper in Warsaw, Poland, standing at 310 meters and featuring 53 floors of office, retail, and leisure spaces. The construction utilized high alumina cement concrete for the foundation and structural works.
“High alumina cement was the ideal choice for the Varso Tower project due to its exceptional mechanical properties, resistance to sulfate attacks, and lower permeability compared to traditional cement,” says the project manager. “We also appreciated its ability to reach high early strength, helping in the acceleration of the construction schedule.”
Case Study 3: Sellafield Nuclear Site, UK
The Sellafield nuclear site is a complex of nuclear fuel reprocessing and nuclear decommissioning plants in Cumbria, UK. The site employed high alumina cement as part of its secondary containment systems, which are designed to prevent the release of radioactive materials.
“High alumina cement has excellent properties for use in the nuclear industry, particularly its ability to resist sulfate and chemical attacks, mitigate the risk of leakage, and withstand temperature fluctuations,” says the engineering team lead. “The use of HAC has been crucial in ensuring the safe containment of nuclear waste and reducing the environmental impact.”
These case studies demonstrate the versatility and reliability of high alumina cement in challenging construction projects that require exceptional strength, durability, and performance. By leveraging the unique properties of HAC, builders, and engineers can achieve optimal results for specialized applications.
Conclusion
In conclusion, high alumina cement offers numerous advantages and unique properties that make it a valuable choice for specialized construction applications. From its exceptional strength and durability to its resistance to chemical attacks and sulfate exposure, HAC exceeds the performance of ordinary Portland cement in many ways.
However, it is essential to consider the potential drawbacks when using HAC, such as its high cost and shorter setting time. Proper handling and curing techniques are also crucial to optimize its performance and prevent shrinkage.
By understanding the chemical composition, properties, and applications of HAC, builders, and engineers can make informed decisions for their projects. With its outstanding performance and versatility, HAC is an excellent choice for refractory linings, precast components, marine structures, and other specialized applications.
As the industry continues to seek more sustainable and environmentally friendly solutions, it is essential to note the potential ecological impact of high alumina cement. However, with proper consideration and implementation of best practices, HAC can still play a significant role in the construction industry.
Overall, we believe that high alumina cement offers a promising alternative to ordinary Portland cement for specialized construction projects. Its exceptional properties and versatility make it an excellent choice for challenging environments and specialized applications. However, it is crucial to weigh the advantages and disadvantages carefully and follow proper handling and curing practices to ensure optimal performance.
Thanks For the Great Attention!
Good Bye & Take Care
Happy Learning
Also, Read,
FAQ
What is high alumina cement?
High alumina cement, also known as HAC, is a specialized type of cement that is composed of high alumina content, typically above 45%. It is produced by heating a mixture of limestone and bauxite at a high temperature, resulting in the formation of calcium aluminate phases. The chemical composition of HAC differs from ordinary Portland cement, giving it unique properties and suitability for specific construction applications.
What are the uses of high alumina cement?
High alumina cement finds applications in various industries and construction projects where high strength, rapid setting, and resistance to extreme temperatures and chemical attacks are required. It is commonly used in refractory linings, precast components, marine structures, and specialized civil engineering projects where ordinary Portland cement may not be suitable.
What are the advantages of using high alumina cement?
HAC offers several advantages over ordinary Portland cement. It has exceptional early strength development, allowing for faster construction schedules. It exhibits excellent resistance to chemical attacks, making it suitable for environments with high levels of sulfates or acidic substances. Additionally, HAC has a low heat of hydration, reducing the risk of thermal cracking in mass concrete structures.
What are the disadvantages of high alumina cement?
High alumina cement has a few disadvantages that need to be considered. It tends to be more expensive than ordinary Portland cement. It also has a shorter setting time, requiring careful handling and proper curing techniques. If not cured properly, it may experience shrinkage and subsequent cracking. It is crucial to follow the manufacturer’s guidelines and recommendations when using HAC.
What is the chemical composition of high alumina cement?
High alumina cement is primarily composed of the calcium aluminate phases, such as monocalcium aluminate (CaO·Al2O3), dicalcium aluminate (2CaO·Al2O3), and tricalcium aluminate (3CaO·Al2O3). The exact chemical composition of HAC may vary depending on the manufacturer, but it typically contains a high percentage of alumina (Al2O3) and a lower amount of silica (SiO2).
What are the properties of high alumina cement?
High alumina cement exhibits unique properties that make it suitable for specialized applications. It has high early strength, allowing for rapid strength development and early formwork removal. HAC has excellent resistance to sulfate attacks, making it a preferred choice in environments with high sulfate concentrations. It also demonstrates good refractoriness, thermal stability, and low permeability, enhancing its durability and resistance to aggressive chemical environments.
How does high alumina cement compare to ordinary Portland cement?
High alumina cement differs from ordinary Portland cement in terms of composition, properties, and applications. Unlike OPC, high alumina cement contains a higher percentage of alumina, giving it superior resistance to chemical attacks. HAC also has a shorter setting time and higher early strength development compared to OPC. However, HAC is generally more expensive and requires specific handling and curing techniques.
What is the IS code for high alumina cement?
The Indian Standard code for high alumina cement is IS:6452-1989. This code specifies the requirements, testing methods, and guidelines for the production, testing, and usage of high alumina cement in India.
What is the initial setting time of high alumina cement?
The initial setting time of HAC typically ranges from 1 to 3 hours, depending on the manufacturer and specific cement formulation. It is essential to monitor the setting time closely and ensure proper handling and curing procedures to achieve the desired results.
What are the applications of high alumina cement in construction?
High alumina cement finds diverse applications in the construction industry. It is commonly used in refractory linings for furnaces, kilns, and incinerators due to its high-temperature resistance. It is also utilized in precast components, marine structures, and specialized civil engineering projects where rapid strength development and resistance to aggressive chemical environments are essential.
What is the environmental impact of high alumina cement?
The production of high alumina cement involves high energy consumption and releases carbon dioxide (CO2) emissions, contributing to the carbon footprint of the construction industry. However, HAC’s durability and resistance to chemical attacks can result in longer-lasting structures, reducing the need for frequent repairs and replacements, which can have a positive environmental impact in the long run. Efforts are being made to develop sustainable alternatives and improve the production processes of high alumina cement.
Can high alumina cement be used with other materials?
HAC can be used with other materials in construction. However, it is important to consider compatibility and adhere to proper mixing ratios and curing techniques. Some materials, such as ordinary Portland cement, may not be compatible with high alumina cement due to differences in setting time and shrinkage characteristics. It is advisable to consult the manufacturer’s recommendations or seek expert advice when using high alumina cement in combination with other materials.
Are there any storage and handling precautions for high alumina cement?
Yes, there are specific storage and handling precautions for high alumina cement. It should be stored in cool and dry conditions to prevent moisture ingress, which can lead to premature setting. High alumina cement should be handled using appropriate protective equipment, such as gloves and goggles, to minimize the risk of skin and eye contact. It is important to follow the manufacturer’s guidelines and recommendations to ensure safe and optimal usage.
Are there any alternatives to high alumina cement?
Yes, there are alternatives to HAC for specific applications. Depending on the requirements and project specifications, alternatives such as calcium aluminate cement (CAC), magnesium phosphate cement (MPC), and geopolymer cement may be considered. It is advisable to consult with engineers or construction experts to determine the most suitable cementitious material for a particular project.
Can you provide some case studies of successful applications of high alumina cement?
Certainly! High alumina cement has been used successfully in various projects around the world. Examples include the construction of refractory linings in industrial furnaces, lining and repairs of chimneys in thermal power plants, and the construction of specialized marine structures such as jetties and seawalls. These case studies demonstrate the unique properties and advantages of high alumina cement in demanding construction environments.